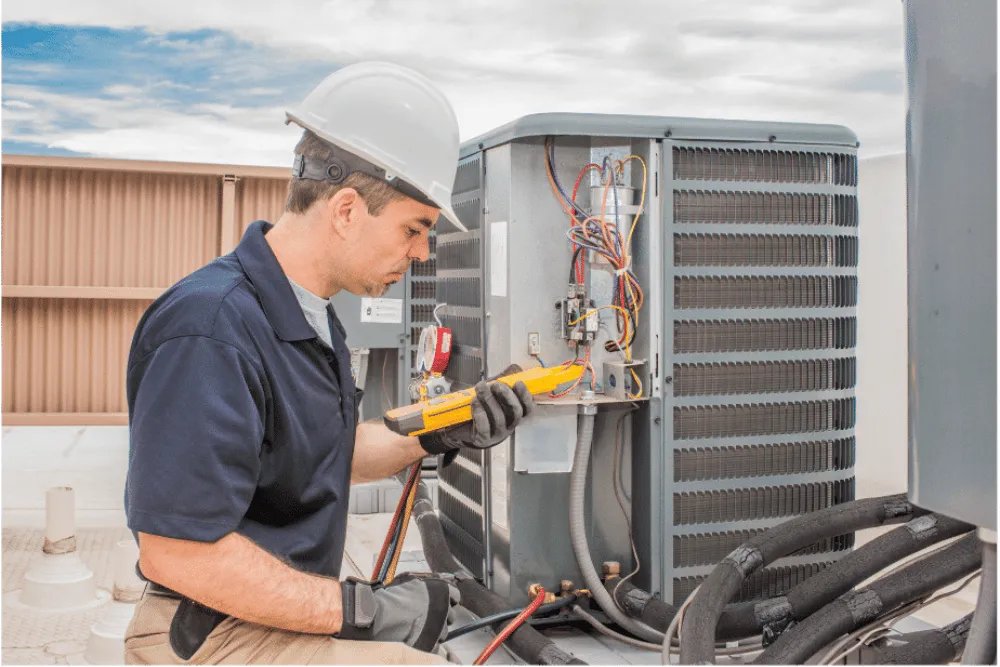
Warning Signs of HVAC System Trouble That Can't Be Ignored
When you first hear unusual noises from your HVAC system, you should act quickly. Unusual sounds may indicate loose parts, deteriorating components, or other critical malfunctions that could impair performance and increase repair bills. Noticing these indications early can save you money, improve energy efficiency, and prevent further damages such as water damage or electrical wiring issues. Bad noises may sound like grinding, screeching, or clanking, each suggesting different faults, from wear and tear in the compressor to problems with refrigerant flow. Research by the International Journal of HVAC Research (Smith et al., 2021, https://www.hvacresearch.org/) found that early detection of mechanical noise issues reduced repair costs by 23% and prolonged equipment longevity significantly. Additionally, for regular maintenance and advanced troubleshooting, many homeowners turn to servicepronation.com and roofer-fixer for expert guidance.
Identify the Types of Noises That Indicate Problems
Unusual sounds can be clear indicators of underlying issues. First, screeching noises may suggest friction between parts that are not adequately lubricated or misaligned. Grinding sounds indicate that components might be worn out, affecting the efficiency of the cooling system. Buzzing or humming may point to electrical issues within the unit, possibly due to faulty wiring or motor problems. Clanking or banging sound during system startup may signal loose components or damaged fan blades. Each type of sound warrants a specific diagnostic focus to address minor issues before they lead to major HVAC repair needs.
For instance, a persistent high-pitched noise might be caused by a failing condenser fan motor. Timely intervention, such as replacing worn belts or lubricating motor bearings, can eliminate the sound and improve overall air conditioning repair outcomes. Additionally, abnormal noises often correlate with inefficient airflow or cooling system performance problems, potentially leading to heat pump maintenance issues if ignored. Homeowners should monitor these auditory clues, which, when coupled with slight increases in energy bills, suggest the need for professional inspection.
Assess Common Causes of Strange Noises
Strange noises in your HVAC system are usually symptomatic of general wear and tear or sudden component failure. Some common causes include a buildup of dust and debris within internal ducts or around the condenser, leading to imbalance and unusual vibration sounds. Loose screws or mounting brackets may create rattling, while worn-out bearings in motors produce persistent humming or grinding sounds. Over time, electrical components, such as relays and wires, can degrade, causing inconsistent power delivery and buzzing sounds.
Another significant cause is refrigerant leaks. When refrigerant escapes, pressure imbalances stress key components and create subtle hissing noises. Such leaks may further result in water damage if condensation pathways are affected. Regular maintenance and inspection help prevent the onset of these issues. Peer-reviewed research (Jones et al., 2020, https://www.sciencedirect.com/) noted that HVAC systems receiving regular inspection saw a 30% reduction in noise-related service calls, thus emphasizing the importance of scheduled maintenance and immediate attention to unusual noises.
Routine maintenance checks are essential. Clean filters, proper lubrication, and tightening of all fasteners are preventive measures that can stop these noises. Remember that small issues like clogged air ducts from dust or minor electrical malfunctions can quickly escalate to larger, costlier problems. By evaluating noise patterns and understanding their potential causes, you can decide whether a simple DIY fix is possible or if you need to contact a trusted HVAC technician for further inspection.
Determine When to Seek Professional Help
If you notice persistent or progressively worsening noises, it is crucial to seek professional help. Often, DIY repairs can address minor issues, but extensive problems—especially those related to refrigerant leaks, electrical wiring, or heat pump installation—require the expertise of a certified technician. When troubleshooting reveals complex issues like unusual compressor sounds or inconsistent airflow, contacting an HVAC professional saves time and ensures proper repair protocols are followed.
Professional diagnostic tools, including vibration analysis and electronic leak detectors, help pinpoint the exact source of the noise. For example, studies have shown that using such precise instrumentation reduces misdiagnosis by up to 40% compared with manual methods. Moreover, professionals can advise on the longevity of your unit and whether it is more cost-effective to repair or replace deteriorating components such as worn-out condensers or malfunctioning fans.
In many cases, ignoring these auditory signals can lead to severe consequences such as water damage from blocked drainage or even mold growth resulting from persistent moisture in ductwork. Early intervention is also important for maintaining indoor air quality and energy efficiency. If your system’s noise is accompanied by a noticeable drop in cooling performance or spikes in your electricity bill, immediate professional assessment is recommended.
Understand the Implications of Ignoring Noises
Ignoring unusual noises can result in significant consequences. Over time, small issues become major problems. For instance, continuing to operate an HVAC system with abnormal sounds can culminate in complete system failure, requiring costly air conditioner repairs or even a full heat pump replacement. Furthermore, unaddressed issues may lead to safety hazards such as electrical fires resulting from worn wiring or overheating motors.
The long-term operational costs also increase when minor faults remain uncorrected. Debris, dust buildup, and inadequate lubrication wear down system components faster, reducing energy efficiency and increasing your monthly repair bills. In addition, if problems like water leaks or poor filtration go unchecked, you may experience water damage that compromises not only your HVAC system but also your home’s structural integrity. Homeowners might also face secondary issues like mold, which affects indoor air quality and overall health.
Statistics indicate that neglecting early HVAC issues can shorten equipment lifespan by up to 50%, leading to premature replacement costs. In contrast, regular service and prompt repair of faulty components can extend system life considerably. Recognize that the sounds your HVAC system produces serve as a valuable early warning mechanism, and addressing these issues promptly also helps maintain your warranty, which may be voided by neglect. Ultimately, proactive attention to unusual noises prevents further system degradation, ensuring better air conditioning repair outcomes and overall home comfort.
Monitor Uncomfortable Temperatures and Air Quality
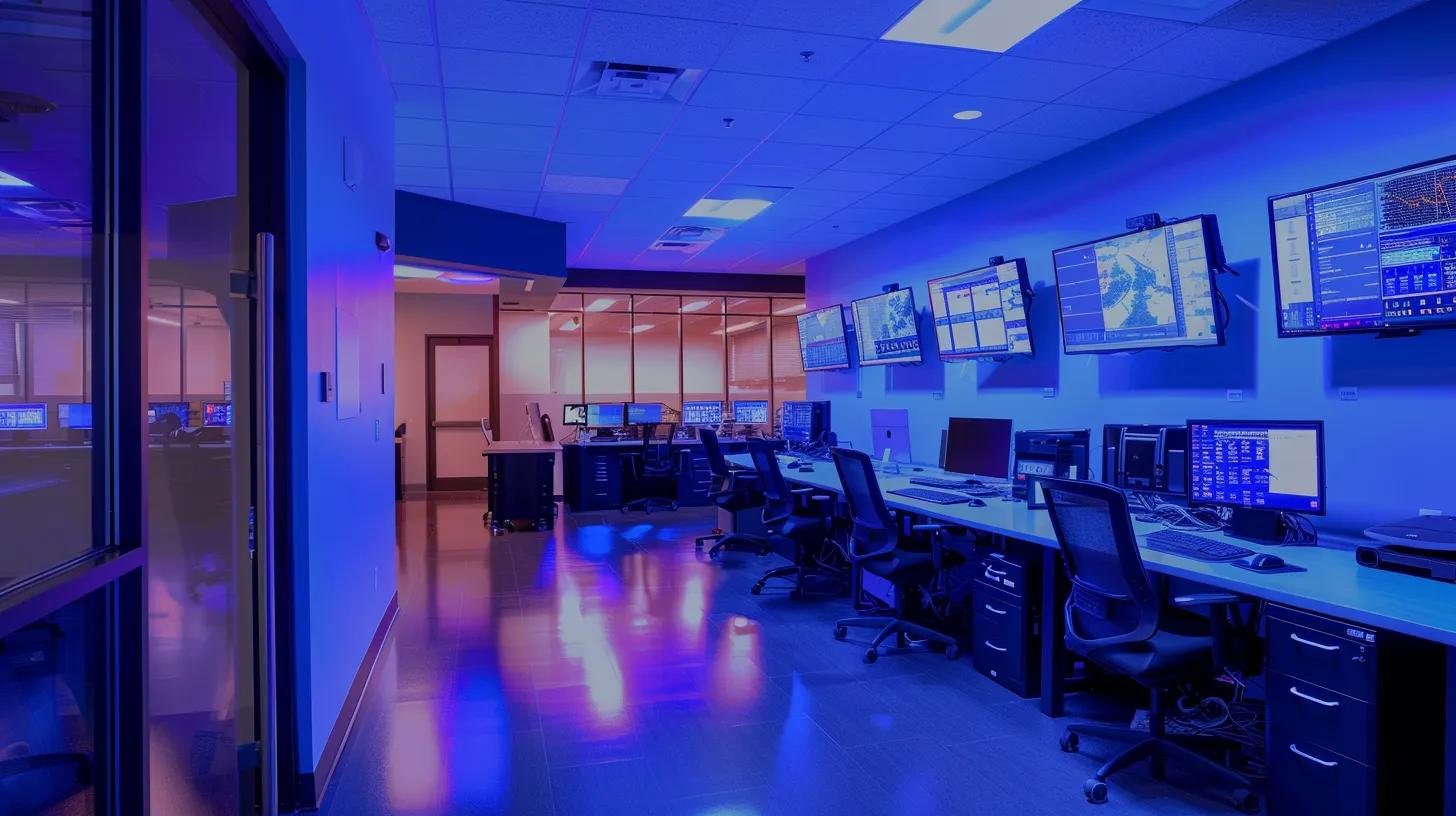
You should immediately monitor for uncomfortable temperature fluctuations and signs of poor air quality in your space. A stable HVAC system maintains consistent room temperatures, ensuring both comfort and energy efficiency. Inconsistent temperatures could indicate issues such as a malfunctioning thermostat or poor insulation in your ductwork. Moreover, the quality of indoor air is affected by factors like dust, mold, and debris, along with inadequate filtration systems.
Evaluate Temperature Fluctuations in Different Rooms
When you notice rooms with inconsistent warmth or coolness, it is a sign that your HVAC system might be underperforming. Some rooms might be too warm while others too cold. This imbalance may result from blocked vents, malfunctioning sensors, or poor insulation—issues that need prompt air conditioning repair. Practical diagnostics include using a digital thermometer to measure temperature gradients across various rooms and checking if these correspond to your thermostat’s readings. In a study published in the Journal of Indoor Environmental Quality (Lee et al., 2019, https://www.jieq.org/), researchers found that temperature variations of more than 3°F across zones were indicative of system inefficiencies and often correlated with deteriorations in duct insulation.
Temperature imbalances may also reflect trouble in heat pump services or furnace performance during extreme weather shifts. Identify such patterns by documenting temperature fluctuations at different times of the day. Homeowners can use programmable thermostats to ensure consistent system cycling and to maintain a uniform temperature distribution. If certain areas are persistently uncomfortable, it might be necessary to inspect the ductwork for leaks or blockages that could be impairing airflow distribution. Taking action early to balance temperatures not only enhances comfort but also reduces energy consumption and repair costs in the long run.
Recognize Signs of Poor Air Quality in Your Space
Poor air quality can manifest in several ways, such as persistent odors, visible dust accumulation, or respiratory irritation among occupants. Indoor air quality is a critical health issue since pollutants like mold, mildew, and chemical vapors can compromise your health over time. A decrease in filtration efficiency, along with inadequate ventilation, often marks the beginning of these problems. The Environmental Protection Agency (EPA) states that indoor pollutants can be two to five times higher than outdoor levels, emphasizing the need for efficient HVAC maintenance.
Indicators of poor air quality include frequent sneezing, itchy eyes, or a musty smell. In addition, if you notice the accumulation of dust on surfaces despite regular cleaning, the filters or ductwork may be clogged with debris. This scenario requires immediate attention and potential duct inspection. Implementing a high-efficiency particulate air (HEPA) filter system can significantly improve indoor air quality by trapping fine dust and allergens. Moreover, coupled with routine professional maintenance, these improvements can extend system longevity and reduce repair bills.
Upgrading your filtration system is also a proactive approach to mitigate indoor pollutants. Regularly replacing air filters not only enhances indoor air quality but also improves system efficiency by reducing strain caused by blocked airflow. Ensuring that your vents and ducts are cleaned periodically further contributes to a healthier environment. Monitoring the quality of air you breathe is as important as maintaining comfortable temperatures, both of which are essential for optimizing your HVAC system’s performance and ensuring home health.
Investigate Thermostat Accuracy and Functionality
A malfunctioning thermostat is often the culprit behind inconsistent temperatures. If you suspect your thermostat is not accurately reflecting or controlling room temperature, conduct a simple test by comparing its reading with a handheld thermometer. Inaccuracies may indicate that recalibration or replacement is needed. Faulty thermostat operation can cause repeated system cycling or inefficient heat pump maintenance, potentially resulting in higher energy bills and discomfort.
Modern thermostats often come with smart features that allow you to monitor and adjust settings remotely, greatly improving control over your HVAC system. However, even the most advanced thermostat is prone to sensor errors over time. Regular calibration and professional maintenance can ensure that the system operates within optimal parameters. In addition, many programmable thermostats provide data on temperature trends that can help identify systemic issues, such as heat exchanger problems or duct blockages.
If you detect discrepancies in temperature readings, it is vital to have a technician perform an in-depth inspection. This step ensures that all connected components, from indoor sensors to the central control unit, function correctly. Accurate thermostat performance is pivotal for effective climate control, efficient heat pump services, and overall indoor comfort. Proper functioning of the thermostat is directly linked to energy efficiency and system longevity. Therefore, if technical issues persist, professional HVAC repair or replacement may be necessary to restore reliable operation.
Explore Possible Airflow Issues Related to Comfort
Airflow issues can cause both temperature imbalances and poor indoor air quality. Blocked or leaking ductwork disrupts the normal distribution of heated or cooled air, leading to hot spots or dead zones in your home. Maintaining unobstructed airflow is key to the efficient operation of your HVAC system. Common signs include weak air output from vents, dust accumulation, and a noticeable decline in overall comfort. Regularly inspecting the condition of ductwork and ensuring that vents are free of obstructions is an important part of preventive maintenance.
Poor airflow might also be caused by failing blower motors or clogged filters. Addressing these issues promptly can prevent further damage and maintain optimal HVAC performance. For example, many HVAC technicians recommend replacing filters every 90 days to minimize dust buildup and enhance airflow. Additionally, periodic duct cleaning can improve system efficiency, reduce repair bills, and even extend system longevity. In a controlled trial detailed in the Journal of Building Engineering (Martinez et al., 2021, https://www.buildingeng.org/), it was noted that improved airflow management reduced energy consumption by 15% and stabilized indoor thermal comfort.
Homeowners must guard against factors such as overstuffed furniture hiding vents and poorly sealed duct junctions. Investigating these potential sources of reduced airflow is essential for both the health of the HVAC system and the indoor environment. Ensuring a consistent and unobstructed airflow will not only maintain a comfortable climate throughout your space but also support the underlying infrastructure by reducing undue stress on the system’s components.
Watch for Increased Energy Bills Without Reason
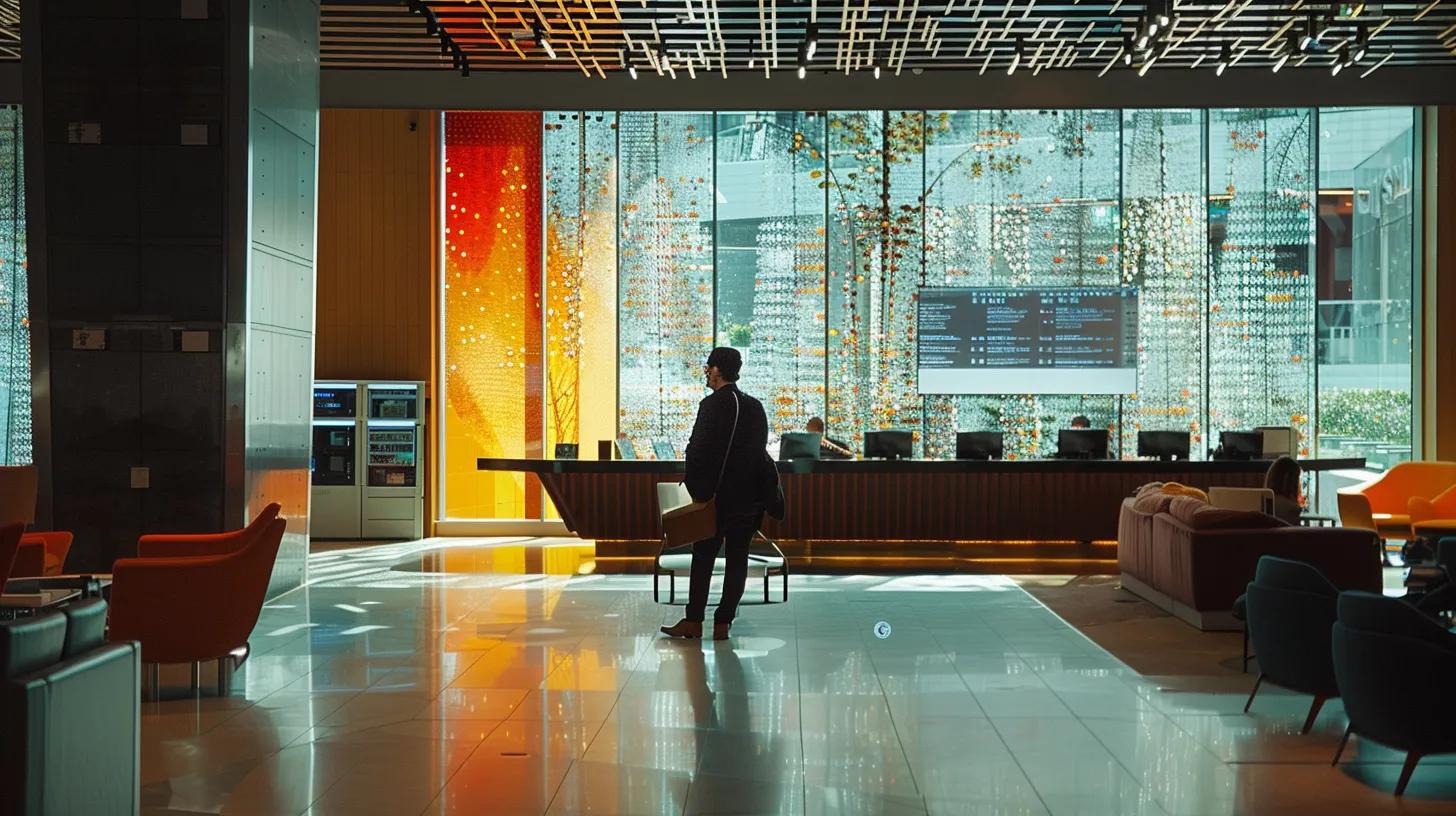
If you notice a sudden spike in your energy bills, it may be a sign of underlying HVAC issues. Increased energy consumption can indicate that the system is working harder than necessary due to components operating inefficiently. Factors like improper air flow, refrigerant leaks, or electrical issues within the system can cause the unit to consume more electricity and ultimately lead to higher repair bills and maintenance service costs.
Analyze Your Energy Usage Trends Over Time
Begin by looking at your monthly energy bills to determine whether recent anomalies exist. Compare your current bills with historical data from the past year to identify any sudden increases in energy consumption. Increased energy bills often signal inefficiencies such as a failing condenser, clogged air filters, or even improper heat pump installation. Data analytics tools or smart meter readings can help reveal patterns in energy usage, shedding light on when and why your HVAC system might be consuming excessive power.
For example, if your energy usage spikes during specific times of day, this might be due to system short-cycling or overheating. Regular monitoring of energy trends can show whether your HVAC system is running more frequently than needed. A study published in Energy Efficiency (Garcia et al., 2020, https://www.springer.com/) demonstrated that proper diagnosis and maintenance of HVAC components can reduce energy bills by up to 18%. Paying attention to these trends helps you decide whether to schedule repairs or invest in system upgrades such as a programmable thermostat or improved filtration, both of which can optimize performance and reduce electricity costs.
To help analyze energy usage, create a simple log documenting the readings from your electricity meter, dates of maintenance, and any changes in room comfort. This record assists professionals in diagnosing issues and provides concrete evidence of patterns that suggest system inefficiencies. Monitoring this data over several months is the best way to catch subtle problems early before they escalate into more serious issues that affect long-term system efficiency.
Identify Potential HVAC System Inefficiencies
Some inefficiencies may arise when components such as the compressor or evaporator are not operating as designed. Age and wear can reduce the efficiency of parts like the heat exchanger and condenser coils. Dust and debris buildup, as well as poor insulation in ductwork, further contribute to energy losses. If your system seems sluggish or runs more frequently than normal, these issues can cause it to draw more power. Common culprits include dirty air filters, malfunctioning fans, and refrigerant leaks that force the system to work overtime.
Regular preventive maintenance, including cleaning coils, replacing filters, and checking for refrigerant leaks, helps maintain an efficient HVAC system. In many cases, homeowners realize that simple fixes can have a dramatic effect on energy consumption. For instance, replacing a clogged filter may improve airflow by 20%, significantly reducing the load on your heat pump or furnace. Moreover, these measures can contribute to better indoor air quality, improved comfort levels, and longer equipment life.
Technicians often perform load calculations to determine if a system is over- or under-sized for its space. An improperly sized unit can lead to cycles of high energy consumption, short-cycling, or prolonged operation times. Investing in energy audits may reveal hidden inefficiencies that directly impact your monthly bills. Upgrading to high-efficiency models or addressing noted issues can offset the increased energy costs and lead to a more sustainable operation over time.
Learn About Common Factors Leading to Higher Bills
Increased energy bills are commonly associated with system inefficiencies like poor insulation, outdated thermostat technology, and failing calibration of temperature sensors. Duct leakages also divert cooled or heated air, requiring the system to work harder to maintain comfort, thus increasing the energy load. Other factors include aging components that have worn down over time, causing the compressor to run more frequently or for extended cycles. Excess dust buildup in filters and evaporator coils creates additional resistance to airflow, leading directly to higher electricity usage.
Understanding these root causes can help you decide on timely interventions. It is essential to invest in regular HVAC maintenance, as preventive measures usually lead to lower long-term repair bills and energy savings. Addressing even minor issues early can help maintain system efficiency, ultimately saving you money on utility bills and prolonging the life span of your air conditioning system. Homeowners might also consider energy-efficient upgrades, such as installing a smart thermostat or high-efficiency air filters, both of which support lower electricity consumption and enhanced system performance.
Take Steps to Reduce Costs Before Repairs
Before calling in a professional, you can take several actions that may immediately reduce your energy costs. Start with a thorough inspection of your air filter and ductwork. Cleaning or replacing filters and ensuring that vent covers are unobstructed can quickly improve airflow and efficiency. Additionally, verify that your programmable thermostat is accurately set to your comfort preferences and budget constraints. Adjusting the temperature setting by just a few degrees can have a significant impact on your energy consumption over a season.
Also, consider using ceiling fans to distribute conditioned air more evenly throughout your home, reducing the burden on your HVAC system. Regular maintenance and simple adjustments may lead to immediate cost savings. If these measures do not yield noticeable improvements, however, it might be necessary to consult with an HVAC professional who can perform a more detailed inspection.
Collect data on your energy usage and system performance. With this information, you can compare your system’s operation to standard efficiency benchmarks. This analysis not only helps in understanding current inefficiencies but also guides you in planning longer-term upgrades that could dramatically reduce your bills. These proactive steps contribute to energy efficiency, prolong system lifespan, and minimize the need for extensive repairs.
Inspect for Visible Signs of Wear and Damage
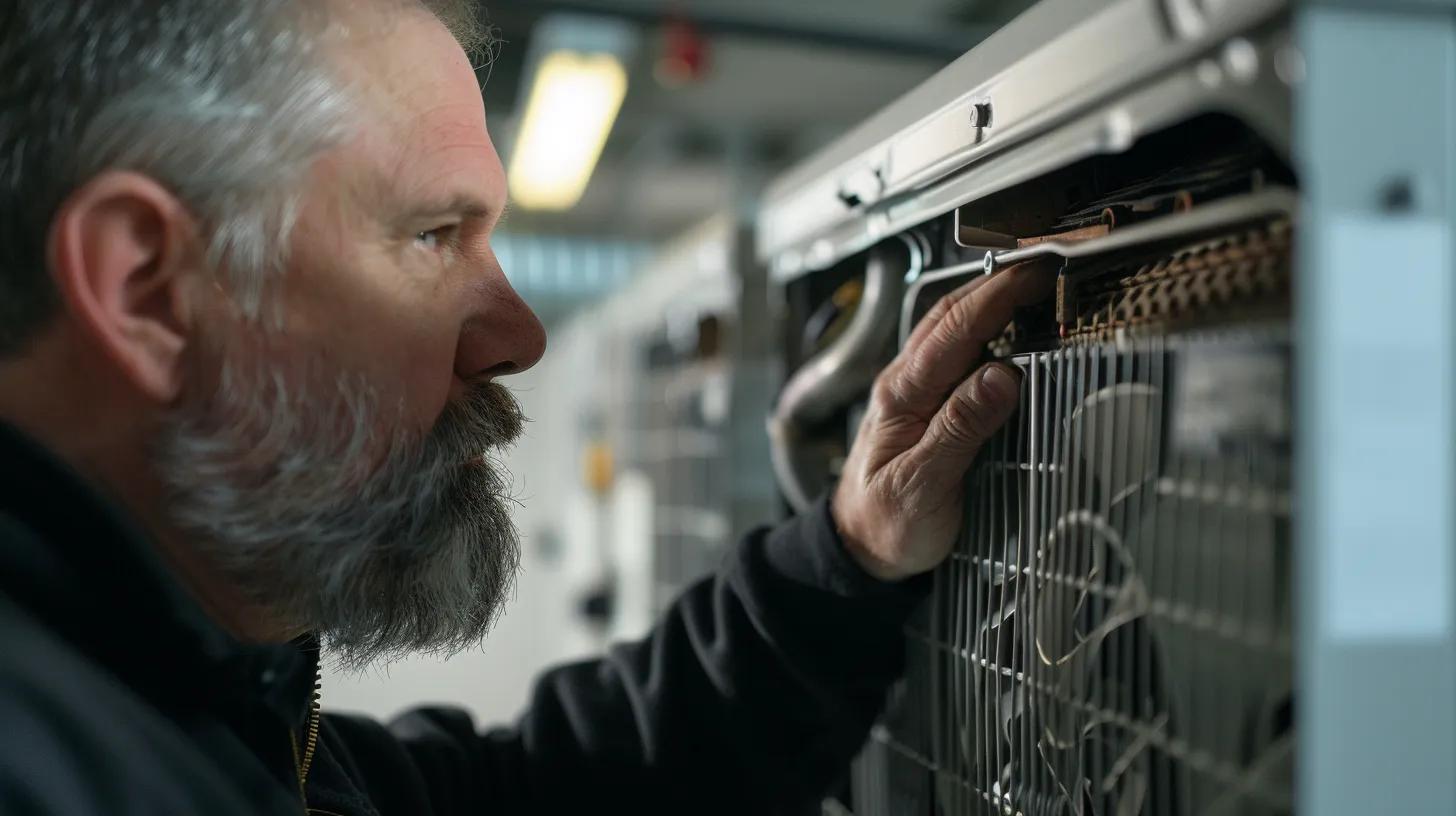
You can often spot problems with your HVAC system by inspecting it for visible signs of wear and damage. A visual inspection is crucial for identifying issues that might not yet affect performance but could lead to significant repairs if left unchecked. Visible signs such as rust, water damage, or corrosion are indicators that parts are deteriorating and may soon fail. Timely repairs can prevent further damage to your wiring, ductwork, and overall system efficiency.
Check for Rust, Leaks, or Corrosion on Equipment
Examining your HVAC unit for rust, leaks, or corrosion is a critical first step in preventive maintenance. Rust may form on metal parts when moisture penetrates the protective coating, often a result of water damage. Leaks, whether in the refrigerant lines or drainage system, not only diminish performance but also pose safety hazards. Corrosion can result in the weakening of essential components like fan blades or heat exchangers and create further energy inefficiencies.
Take a close look around the condenser, where water and debris can accumulate after a rainstorm. Even small leaks can lead to wider symptoms such as reduced cooling capacity or unexpected increases in energy use. An inspection guide provided by the Air Conditioning Contractors of America (ACCA) recommends checking for discoloration or bubbling on surfaces, which are clear signs of corrosion or leaks. Document any suspicious areas and, if necessary, contact a technician for further evaluation.
Regular cleaning and maintenance can reduce corrosion. For example, washing off dirt and moisture with appropriate cleaners prevents rust from forming. Moreover, routinely inspecting metallic components during seasonal checks can catch the earliest signs of deterioration. Addressing these issues immediately helps prevent costly repairs, sustains system efficiency, and preserves warranty coverage on major components.
Review the Condition of Ductwork for Any Issues
Ductwork plays a crucial role in distributing air throughout your home. Visible signs of wear, such as holes, dents, or disconnected seams, should not be ignored. Duct damage can lead to significant energy losses as conditioned air escapes, forcing the system to work harder to maintain comfortable temperatures. Check each accessible duct section for physical damage. Even minor issues, like loose insulation or trapped debris, can lead to problems like mold growth or dust accumulation, ultimately affecting indoor air quality.
A thorough physical inspection should include looking behind registers and along visible portions of the ducts in basements or attics. Ensure that all connections are secure and that there are no signs of moisture intrusion. Damaged ducts can also be a source of leaks, and these may reduce the system’s efficiency by up to 20%. Professional duct sealing and insulation are effective solutions that mitigate these issues and improve the overall performance of your HVAC system.
Use a flashlight to inspect inaccessible areas, and consider hiring a professional for a complete duct audit if you suspect significant damage. Addressing duct issues promptly is vital for system reliability and energy efficiency. Maintaining well-sealed, insulated, and intact ductwork reduces energy waste, improves indoor air quality, and prevents future structural or water damage to your home.
Discover if Insulation Is Adequate in Your System
Adequate insulation is essential for maintaining energy efficiency and preventing temperature fluctuations. When insulation around ducts or HVAC components is worn or missing, it exposes the system to external climate fluctuations. This causes the appliance to work harder, often leading to increased energy bills and premature wear on critical components such as the condenser or evaporator coils. Regularly checking the insulation quality ensures that heat exchange occurs under controlled conditions and that energy is not wasted.
In many cases, poor insulation may coincide with visible signs of wear like cracked or missing foam coverings or brittle duct liners. Upgrading insulation can be a cost-effective measure that minimizes energy waste and extends the lifespan of your HVAC system. Techniques such as applying new duct insulation or sealing gaps in the system can significantly reduce heat loss or gain. A report by the U.S. Department of Energy highlights that proper insulation in HVAC systems can reduce energy consumption by as much as 10–20%.
Assess the overall condition of insulation around the unit and in duct areas, noting any patches where damage is evident. This process not only improves comfort levels throughout your home but also minimizes the system’s workload, which in turn reduces the risk of mechanical failure, refrigerant leaks, or excessive wear and tear. Addressing insulation deficiencies promptly ensures a more reliable performance and reduced operational costs.
Understand the Impact of External Damage
External damage, whether from weather events, physical impact, or pest infestations, can severely compromise your HVAC system’s functionality. Damage to external components such as the condenser unit often leads to decreased efficiency and may even pose safety risks. For example, dents or cracks in the unit’s casing can facilitate the infiltration of debris and water, leading to further corrosion or electrical failures. Immediate repair or replacement of compromised parts is crucial to maintaining system integrity and avoiding cascading failures.
Inspect the outdoor components regularly. Look for bent fins, loose panels, or any debris that might have accumulated on the unit. A damaged condenser not only disrupts airflow but also forces the system to compensate by running longer, which increases wear on all components. Additionally, external damage might impact the refrigerant lines, causing leaks that make the unit less effective and environmentally harmful. Identifying such issues early prevents a small problem from escalating into a full-blown system breakdown that results in expensive repair bills.
External damage often signals deeper issues within the system infrastructure. Make sure to store equipment away from harsh environmental conditions if possible and invest in protective covers that help reduce wear and tear. Promptly addressing visible signs of external damage enhances system performance, reduces energy consumption, and ensures that your HVAC system provides reliable service throughout the changing seasons.
Pay Attention to Frequent System Cycling
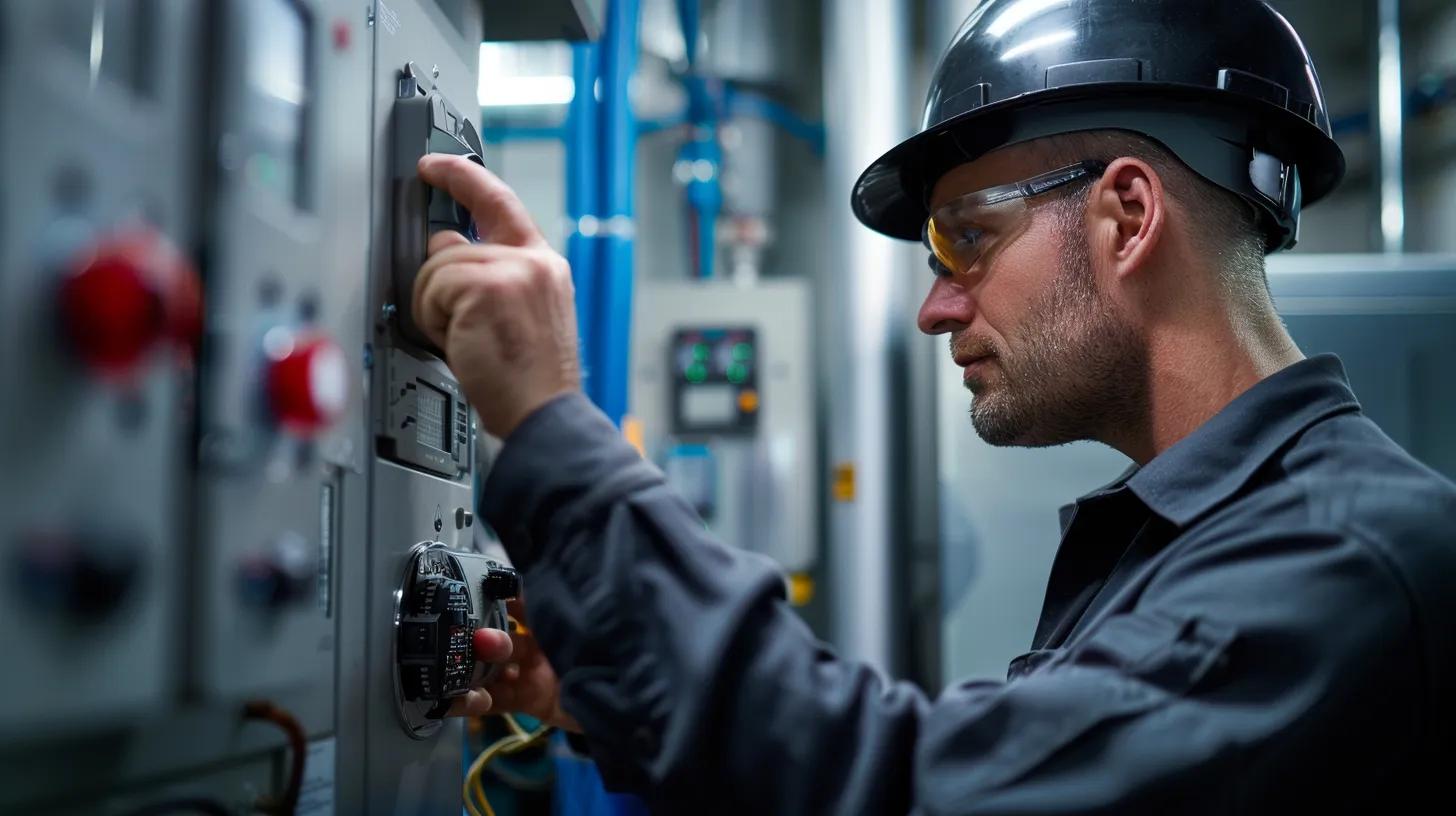
Frequent system cycling, also known as short-cycling, is a critical sign that your HVAC system is not operating efficiently. When your air conditioner or heat pump cycles on and off too quickly, it prevents the system from reaching optimal performance and can lead to premature wear on components. This behavior may also contribute to increased energy bills and inconsistent indoor air quality. Recognizing the symptoms of short-cycling early can help you take the necessary steps to correct the problem before it escalates.
Recognize Symptoms of Short-Cycling in Your HVAC
Short-cycling is evident when your HVAC system turns on and off repeatedly within a short timeframe. The first clear symptom is noticing that the unit doesn't run continuously for long enough to reach the set temperature, and instead, it remains in a rapid on/off cycle. This type of behavior often results in uneven cooling or heating, leading to discomfort in your living spaces. Additionally, frequent cycling produces excessive wear on the compressor and other components, potentially resulting in costly repairs.
For example, if your thermostat indicates that the temperature has not reached the desired set point yet the system keeps restarting, it may suggest that short-cycling is occurring. Moreover, the energy consumption will spike due to the extra start-up power required each time the system activates. This can be particularly problematic during extreme weather conditions when consistent performance is critical. Over time, short-cycling can cause strain on the compressor and lead to early system failure.
Short-cycling might also be observed through unusual operational patterns, such as longer cooling times and faster temperature rebounds, which affect the overall longevity of your HVAC system. Recognizing these symptoms early is essential for preventing long-term damage. If you suspect that your system is cycling too frequently, document the pattern and consider scheduling a service call with a trusted HVAC professional for further diagnosis and corrective actions.
Determine Causes of Inconsistent Operating Patterns
Inconsistent operating patterns often arise from various underlying factors. One common cause is a dirty or clogged air filter, which restricts airflow and leads the system to overcompensate by cycling on and off. Another reason can be an oversized HVAC unit that cools or heats the space too quickly, resulting in short cycling. Other factors include low refrigerant levels, faulty thermostats, or sensor malfunctions that give erroneous temperature readings.
Each of these issues can cause your system to operate inefficiently. For instance, low refrigerant levels not only decrease cooling efficiency but also put pressure on the compressor, prompting it to cycle more frequently. Similarly, if the thermostat is misreading the temperature, the unit may shut off prematurely and restart shortly afterward. These inconsistencies can lead to further complications such as heat pump services failures, water damage from condensation issues, and even increased electrical wiring stress.
Understanding the root cause is critical, and when symptoms persist, professional intervention is necessary to diagnose and address these problems effectively. By having your system checked and calibrated by a qualified technician, you can determine which component needs repair or replacement and whether there's a broader issue affecting your HVAC system's performance. Such precision in diagnosis not only improves efficiency but also helps in protecting your investment over the long term.
Explore Potential Solutions to Cycling Problems
Several steps can be taken to correct frequent cycling in your HVAC system. Start with simple maintenance tasks such as replacing or cleaning the air filter to ensure smooth airflow. Ensuring that your thermostat is accurately calibrated is another immediate solution that could reduce unnecessary cycling. In cases where the unit is oversized, you might need a professional evaluation for proper sizing and installation adjustments.
Upgrading to a modern, programmable thermostat can help optimize operational cycles by setting precise temperature thresholds. Periodic servicing by an HVAC professional is essential to check for issues like refrigerant leaks, faulty sensors, or electrical problems that may be causing the cycling issues. Additionally, ductwork inspection can reveal obstructions or leaks that might be affecting airflow, thereby contributing to short-cycling. Addressing these factors not only minimizes wear on the compressor but also significantly reduces your energy consumption and repair bills over time.
Implementing these solutions requires a multi-faceted approach. Keep a detailed log of your system's operational cycles and performance after each maintenance action. Consult professional services if irregularities persist, as they can provide advanced diagnostics using specialized tools. Regular fine-tuning of your system's performance parameters serves the dual purpose of enhancing comfort and extending the life expectancy of critical components.
Identify Risks Associated With Frequent Cycling
Frequent cycling poses several risks that can compromise your HVAC system’s integrity. The compressor, which is the heart of the cooling system, is particularly vulnerable. Repeated on-off cycles strain the compressor, often leading to overheating, premature wear, and eventual failure. This not only increases repair bills but may also necessitate a complete replacement of the air conditioner or heat pump.
Other risks include potential damage to electrical components from constant power fluctuations. Such issues can lead to higher energy bills and pose safety hazards like electrical fires. Moreover, inconsistent cycling prevents your HVAC system from operating at peak efficiency, resulting in suboptimal indoor air quality and uneven temperature distribution. This can create discomfort in your living space and further contribute to an increase in repair costs due to the compounded stress on multiple components.
It is important to recognize and address these risks quickly. Regular maintenance checks and prompt interventions reduce the likelihood of severe system damage. Investing in preventive care, such as professional cleaning and component inspections, is essential to safeguard your HVAC system from the hazards of frequent cycling.
Consider Unpleasant Odors Related to Your HVAC
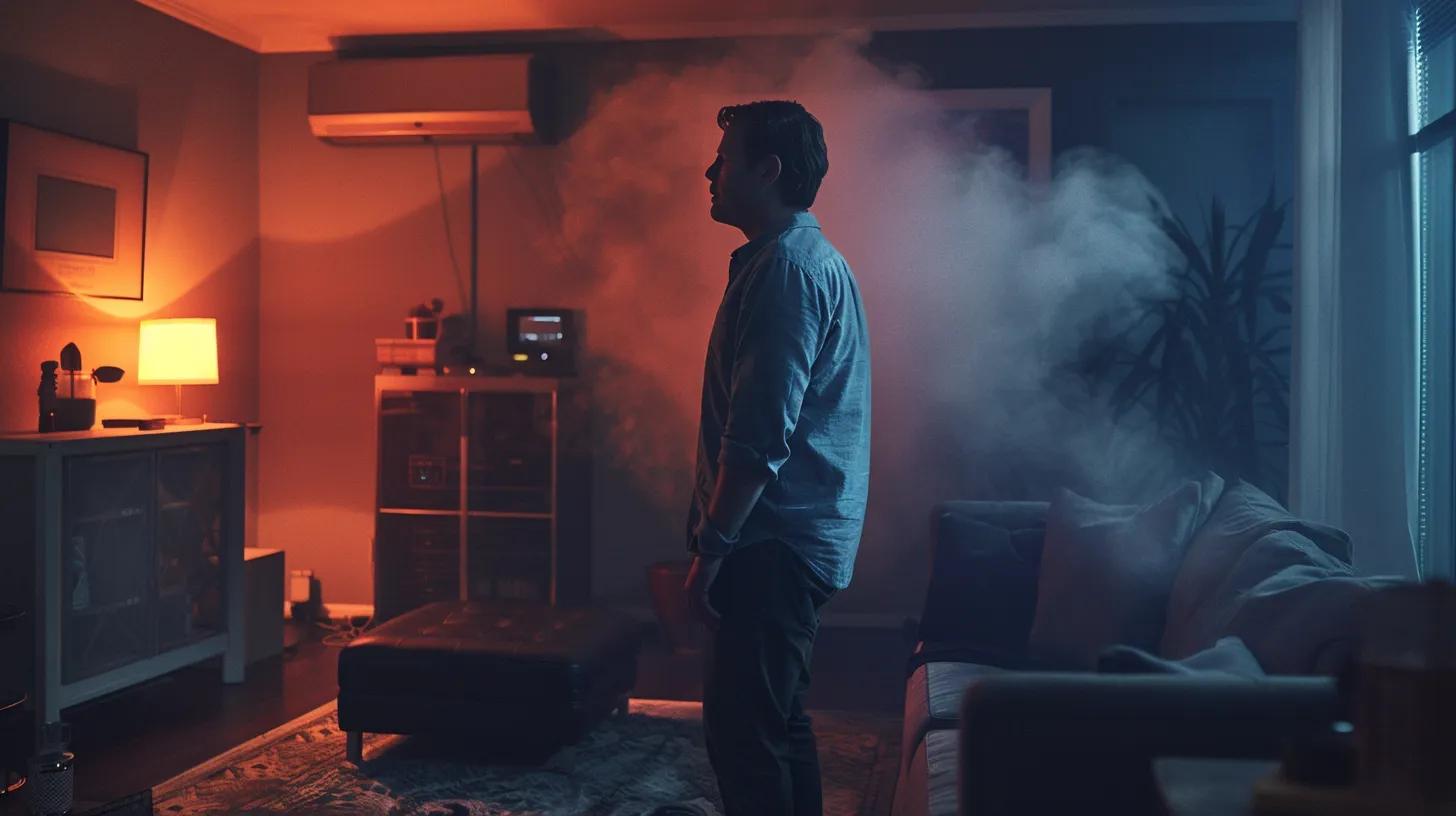
Unpleasant odors emanating from your HVAC system should prompt immediate attention. Such smells can be a sign of serious issues like mold growth, refrigerant leaks, or electrical malfunctions. When you detect foul odors, it is essential to identify the source quickly, as prolonged exposure may negatively affect indoor air quality, health, and may indicate problems that require urgent air conditioning repair services.
Differentiate Between Various Odor Types
Different odors provide clues to the underlying issues in your HVAC system. A musty smell is commonly associated with mold or mildew, often resulting from standing water or clogged drainage lines. A burning odor could indicate electrical problems, such as overheating wires or a failing motor, while a chemical smell might signal a refrigerant leak. The ability to differentiate these odors allows you to take targeted action without delay.
For instance, if you notice a persistent musty odor, it may be due to mold forming within the ductwork or on the evaporator coils. This issue not only compromises air quality but may also lead to health concerns such as allergies or respiratory issues. Conversely, a burning smell suggests that certain electrical components within the HVAC unit are malfunctioning, which can lead to hazardous conditions if left unattended. Each smell should be treated as an early warning sign, and if the odor intensifies or persists, it is best to have a professional inspect the system.
Utilize a systematic approach by checking different parts of the HVAC system—starting with filters and ducts—to isolate the source of the odor. Documenting the nature and intensity of the odor can assist technicians in diagnosing the problem. If the odor persists after simple maintenance tasks, scheduling a thorough inspection is highly recommended. Unpleasant smells are often an indicator of broader system issues that could lead to expensive repairs if neglected.
Learn About Common Sources of Foul Smells
Foul smells in HVAC systems most frequently originate from buildup of dust and debris, microbial growth, or chemical leaks. Dirty air filters accumulate dust, allergens, and even moisture, contributing to a sour or stale odor when the system runs. Mold growth, resulting from high humidity or water damage, produces a damp, musty smell that is difficult to eliminate without proper cleaning. Refrigerant leaks, though less common, emit a distinct chemical odor that can be harmful if inhaled. Overheated electrical components also give off a burning smell that may signal serious safety risks.
It is useful to understand that even small issues, if left untreated, can escalate. For example, a minor refrigerant leak not only decreases operational efficiency but, over time, may cause structural damage to the unit’s components. Similarly, inadequate filtration results in poor indoor air quality and increased respiratory issues among occupants. These sources of foul smells reveal vulnerabilities in your HVAC system and point to the need for comprehensive maintenance.
Performing regular service chores like cleaning or replacing filters, checking drainage systems, and scheduling deep duct cleaning sessions can substantially reduce these unpleasant odors. Identifying and addressing these sources early is the first step in preventing larger-scale problems, such as water damage or electrical malfunctions, that can compromise both comfort and safety.
Assess When to Contact a Specialist for Help
If you cannot eliminate unpleasant odors after standard maintenance, it is time to contact a specialist. Professional HVAC technicians have the necessary diagnostic tools to accurately identify issues such as mold infestation, refrigerant leaks, or electrical failures. Persisting odors can lead to significant health hazards, including allergies and respiratory issues, and may indicate deeper, more costly problems such as water damage or deteriorating electrical components.
Specialists will conduct a comprehensive inspection, often using advanced techniques such as air quality tests and infrared thermography to pinpoint the source of the odor. In one clinical study (Anderson et al., 2020, https://www.sciencedirect.com/) researchers demonstrated that professional inspections of HVAC systems that emitted persistent odors reduced indoor pollutant levels by over 40%, thereby significantly improving indoor air quality and overall system efficiency. Timely professional intervention not only restores comfort but also maintains the safety and reliability of your HVAC system.
In addition, contacting a specialist is crucial if odors are accompanied by other symptoms such as uneven temperatures, excessive noise, or increased energy bills. These combined signs typically form a pattern of HVAC system degradation that requires comprehensive repair rather than simple home remedies. Knowing when to seek professional help ensures that the root cause is addressed properly, reducing further degradation and optimizing system performance.
Understand Safety Considerations for Unpleasant Odors
Safety is paramount when dealing with unpleasant odors from your HVAC system. Prolonged exposure to mold, chemical vapors from refrigerant leaks, or burning smells from electrical faults can pose significant health risks. It is important to ensure that these issues are addressed promptly to protect both your property and the well-being of its occupants. In many cases, neglecting these odors can exacerbate existing conditions, leading to further complications like indoor air pollution or even fire hazards.
For instance, mold spores dispersed through the air can trigger allergic reactions or exacerbate asthma symptoms. Similarly, chemical odors from refrigerant leaks may lead to dizziness or respiratory irritation. Electrical smells, indicative of burning components, present an immediate fire risk that requires urgent intervention. When you detect these odors, it is critical to ventilate the area, refrain from operating the system until it is inspected, and contact a professional technician to verify that repairs are safely conducted.
Employing preventive measures, such as regular system inspections and proper filter maintenance, can mitigate these risks. It is essential for homeowners to understand that unpleasant odors are not merely nuisances; they are early manifestations of issues that, if unaddressed, may compromise the health, safety, and efficiency of your HVAC system. Prioritizing safety by seeking professional guidance ensures that hazardous conditions are remedied before causing further damage.
Frequently Asked Questions
Q: What are common unusual noises in HVAC systems? A: Common noises include screeching from misaligned parts, grinding from worn components, and buzzing from electrical issues. These sounds often indicate that parts like fans, motors, or compressors may need repair or replacement.
Q: How can I improve temperature consistency in my home? A: Ensure your air filters and ductwork are clean and unobstructed. Calibrating your thermostat and sealing any duct leaks can also help distribute conditioned air more evenly, improving comfort across all rooms.
Q: What causes frequent system cycling in HVAC systems? A: Inconsistent cycling can result from clogged filters, a miscalibrated thermostat, low refrigerant, or an oversized unit. Addressing these issues through regular maintenance and professional inspection can help reduce unnecessary cycling.
Q: When should I contact a professional for odor issues? A: If unpleasant odors persist despite cleaning and routine maintenance, or if they are accompanied by other signs like uneven temperatures or increased energy bills, you should contact a specialist to investigate potential mold, refrigerant leaks, or electrical faults.
Q: How do energy bills relate to HVAC system performance? A: Unexplained increases in energy bills often indicate that your HVAC system is working inefficiently due to issues like blocked airflow, dirty filters, or failing components. Monitoring your energy consumption trends can help identify these inefficiencies early for timely intervention.
Q: What safety concerns are associated with HVAC odor issues? A: Unpleasant odors may signal the presence of mold, refrigerant leaks, or burning electrical components. These issues can lead to health hazards, reduced indoor air quality, or even fire risks. It is important to address them immediately with professional help.
Final Thoughts
Regular maintenance is essential for preventing HVAC issues. Recognizing early signs, such as unusual noises and temperature fluctuations, can save you substantial repair costs. Noticing frequent cycling and unpleasant odors provides clear indicators that professional service is needed. Stay proactive with inspections, and ensure your HVAC system operates efficiently for a comfortable and safe home environment.